- Sommaire
-
-
-
- MONOCUISSON
- par
Smart2000
|
-
-
-
-
-
-
- Monocuisson : Once firing
(Eng)
-
- En céramique
émaillée, la monocuisson consiste
à cuire simultanément une terre crue et
sa glaçure. C'est le procédé
céramique qui offre la meilleure performance
énergétique, mais c'est aussi une
technique pointue qui demande une maîtrise
parfaite et de savantes mises au point pour
réaliser une production de
qualité.
- En règle
générale, en vaisselle ou en poterie, la
monocuisson est utilisée pour produire des
objets bon marché dont les critères de
qualité ne sont pas très rigoureux. La
monocuisson bien maîtrisée est sourtout
le fait de productions industrielles
entièrement basées sur cette technique
comme celles du carrelage et du sanitaire... et de
quelques exceptions en vaisselle.
-
- A l'heure où le
coût des énergies explose, que ce soit
pour l'électricité ou le gaz, les
industriels et les artisans ont tout intéret
faire le maximum d'économies dans le domaine de
la cuisson qui est le plus gros poste
énergivore mais indispensable dans la
production de céramique. Cuire "malin" devient
la règle. Utiliser moins d'énergie,
récupérer la chaleur perdue, utiliser
des sources d'énergies durables, modifier les
compositions pour abaisser les températures de
cuisson, diminuer les charges passives
(réfractaires), isoler pour limiter les
déperditions, etc...
-
-
- Technique 2 ou 3 en 1
:
-
-
- Dans certains cas la
monocuisson peut aussi permettre de réaliser
simultanément la cuisson de la terre, du
décor et de la glaçure, imbattable au
niveau coût de cuisson.
-
- Le meilleure exemple cette
application se trouve dans la fabrication industrielle
des carrelages, où les carreaux pressés
en pâte sèche sont
sérigraphiés avec une ou plusieurs
couleurs avant d'être émaillés par
turbine puis passés dans un four à
cuisson rapide. La production en quelques heures des
carreaux décorés en monocuisson se
prête particulièrement bien à
cette technique, mais elle n'a été
rendue possible et fiable que grâce à
d'importantes recherches sur la glaçure et sur
la pâte. On parle alors de monocuisson
"rapide".
-
- Un autre exemple de
monocuisson 3 en 1 en vaisselle était celui de
la fabrication industrielle des mugs
décorés. Décoration
jusqu'à 4 couleurs posées en
sérigraphie directe sur les pièces crues
sèches émaillées par aspersion
puis passage en cuisson dans les four tunnels de
l'usine "Staffordshire Tableware" de Stoke-on-trent
(GB) dans les années 1995 où plus d'un
millions de mugs destinés à la grande
distribution étaient ainsi produits par
semaine.
-
- Une exception
Française pour la vaisselle, la
société Revol à St-Uze
maîtrise parfaitement la monocuisson rapide de
la porcelaine émaillée. Elle produit une
porcelaine culinaire de qualité sur une gamme
d'articles aux lignes modernes.
-
- Le procédé de
monocuisson permet de réaliser 2 à 3
opérations céramiques fondamentales en
une seule cuisson. Beaucoup d'industriels tentent
la réalisation de céramiques en
monocuisson, l'enjeu économique est très
important, surtout lorsque les produits doivent rester
abordables et concurencer les importations à
faible coût de main d'oeuvre.
-
- Les potiers de grès
travaillent souvent en monocuisson, les
glaçures non frittées permettent ce
procédé de même que les
glaçures au sel (voir cette page :
https://smart2000.fr/glacures_au_sel.htm).
-
- Mais pour pouvoir profiter
pleinement des effets "cost-réducteurs" de la
monocuisson, il faut vraiment disposer de solutions
céramiques parfaitement adaptées
à ce procédé, car en cas de
défaillance la monocuisson peut s'avèrer
très destructrice et ruiner totalement toute
une production.
-
-
- ABC... de la
monocuisson :
-
-
- A) La glaçure doit
avoir une température de fusion la plus tardive
possible afin de permettre aux gaz du tesson de
s'échapper sans endommager la surface
émaillée (sinon il se produit des bulles
et des cratères dans la
glaçure).
-
- Les glaçures de
grès ou de porcelaine seront
constituées de matières premières
crues plutôt que de frittes afin que la fusion
soit plus tardive. Le choix de matières
fondantes (feldspaths) à un niveau de finesse
moindre aidera à faire reculer le point de
"fermeture"
(*)
de la glaçure. Les coûts de telles
glaçures sont ainsi parmi les plus bas, les
matières crues étant bien meilleur
marché que les frittes.
-
- (*) Point de fermeture
d'une glaçure : température à
partir de laquelle l'état de la glaçure
empêche le passage des gaz du tesson
-
- Pour les faïences et
les tessons poreux on recherchera des frittes
à point de ramollissement élevé
(> 800°C). Ces frittes sont potassiques, elles
contiennent un taux de zinc et de calcium
élevé, peu ou pas de bore, un peu de
magnésium.
-
- Voici un tableau des
compositions de frittes à point de
ramollissement > à 800°C :
-
Oxyde
|
Fourchette
du % en masse
|
Fourchette
en moles (formule de
Seger)
|
SiO2
|
58 à
66
|
2.100 à
2.750
|
B2O3
|
0 à
2
|
0 à
0.170
|
Al2O3
|
4 à
9
|
0.090 à
0.190
|
K2O
|
2 à
6
|
0.050 à
0.140
|
Na2O
|
0 à
1
|
0 à
0.040
|
CaO
|
10 à
15
|
0.420 à
0.640
|
MgO
|
1 à
3
|
0.060 à
0.180
|
ZnO
|
9 à
11
|
0.200 à
0.300
|
-
- Ces frittes
spécifiques ne sont pas toujours faciles
à trouver au détail, elles ne sont pas
courantes dans les catalogues de produits usuels pour
la céramique. En s'adressant directement aux
fabricants un approvisionnement par quantité
minima est souvent possible.
-
-
- Pour toutes les
glaçures : l'application par
pulvérisation favorisera un point de fermeture
plus élevé que par trempage ou aspersion
(Voir l'article sur la tension superficielle et
l'émaillage : https://smart2000.fr/tension_superficielle_email.htm
.
-
-
-
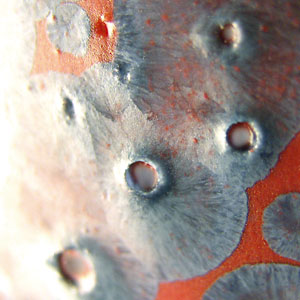
-
- Exemple de
bullage dans une glaçure cristalline
mate
- cuite en
monocuisson sur tesson de porcelaine dû à
l'air de retrait
- (C'est le cas
d'une pâte à porcelaine feldspathique
à qui expulse des
- gaz au dessus de
1150°C sous l'effet du fort retrait de la
pâte lorsque la glaçure est fondue et
fermée)
-
-
-
-
-
-
-
- B) La vitesse de
montée en température doit être
bien dosée pour que les gaz du tesson ne
s'échappent pas trop
brutalement.
-
- Départ de l'eau :
La
montée à 300°C doit être
lente pour faciliter le départ de l'eau
résiduelle (c'est dans cet intervalle que les
risques d'explosion des pièces sont
importants). Les produits doivent être
parfaitement secs à l'enfournement. Une
montée à 100°C par heure convient
dans beaucoup de cas.
-
-
- Décomposition du
carbonate de calcium (craie, marbre) : En
présence d'air, à partir de 800°C
le carbonate de calcium se décompose en oxyde
de calcium, CaO (chaux vive) et gaz carbonique, CO2.
-
- CaCO3 (800-900°C)
==> CaO + CO2, Cette réaction est
normalement achevée à 900°C.
-
- Au delà de 900°C
l'oxyde de calcium se combine avec les
éléments du tesson (la silice,
l'alumine, le fer...) et forme des silicates, des
aluminates, des silico-aluminates, des
ferrites....
-
- Le volume de gaz carbonique
produit est très élevé, 100g de
craie produisent environ 44g de caz carbonique. Ces
44g de gaz carbonique à la température
de 900°C et à la pression
atmosphérique ont un volume de 218 litres... Il
est donc impératif qu'un tesson
émaillé renfermant de la craie ou de la
dolomie soit cuit lentement entre 800°C et
900° et que la glaçure soit fermée
au delà de cette plage de la cuisson (Cas des
faiënces calcaires, pouvant contenir
jusqu'à 20-25% de craie ou de
dolomie).
-
- La décomposition par
combustion des produits carbonés (Charbon des
ball clay, matières organiques) et des sulfures
a lieu à partir de 700-850°C, produisant
du gaz carbonique et du dioxyde de soufre. Pour que
cette réaction soit rapide et complète
il convient de bien oxygèner le four avec un
excès d'air convenable (ouvrir la
cheminée du four). Dans le cas contraire une
partie du carbone et des sulfures
incomplètement oxydés subsista et pourra
continuer à se décomposer à plus
haute température après la fusion de la
glaçure.
-
- Cette plage de
température devra être passée avec
prudence. Un palier assez long vers 850-900°C
suivi d'une montée lente à 1000-1050
permettra d'évacuer les gaz en limitant les
dommages à la couche de glaçure.
- Pour les glaçures
trop précoces à la fusion ce type de
précaution peut s'avèrer inutile, car
une glaçure fondue offre peut de
résistance à la pression des gaz du
tesson. Généralement les gaz
s'échappent du tesson par bouffées, en
empreintant les passages les plus faciles (les pores
les plus gros, les petites fissures...) et font
irruption à travers la glaçure fondue en
produisant des bulles. Plus le dégagement de
gaz est violent et plus les bulles sont grosses.
-
- C) Les pâtes
doivent contenir le moins possible de composés
produisant des gaz à haute température
(pour les températures >> 1000°C)
-
-
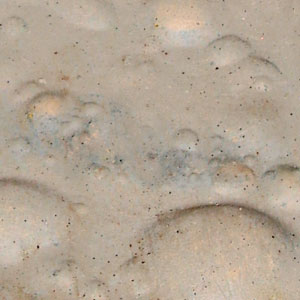
-
- Pâte de
grès de St-Amand boursouflée par une
cuisson trop rapide et un dégazage
difficile
-
-
- Les pâtes qui
contiennent des argiles chargées en
matières organiques du type " ball clay "
présenteront plus de difficultés en
monocuisson. Leur haute teneur en carbone (morceaux de
charbon ou matières organiques) et parfois en
soufre (sulfures) en fait des tessons qui rejettent
beaucoup de gaz, et l'extrême finesse des
particules argileuses qui les composent constituent un
tissu serré qui freine le passage des gaz, ce
qui peut conduire à des dégagements
spasmodiques de gaz avec risque de bulles.
-
- Des dégraissants
(chamotte, silice) ajoutés à la terre
facilitent aussi le passage des gaz à travers
le tesson lors de la cuisson.
-
- PERTE au FEU
:
-
- Pour avoir une idée
des transformations gazeuses se produisant pendant la
cuisson dun produit, on peut calculer sa perte
au feu. Cest à dire connaître sa
perte de masse en pesant un échantillon avant
et après cuisson. Le calcul sécrit
comme suit :
-
- PF % = 100 * ((poids avant
poids après) / poids avant)
-
- Note : La perte de poids
indiquée est toutefois approximative car il
peut aussi y avoir des réactions faisant
reprendre du poids à léchantillon
lors de la cuisson. Un métal tel que le fer
initialement présent sous forme doxyde
ferreux, FeO, peut se transformer tout ou
partiellement en oxyde ferrique ou hématite,
Fe2O3, sous leffet de la chaleur et de
latmosphère oxydante.
- La prise de poids de FeO
lors de sa transformation en Fe2O3 est de lordre
de 11%. Pour les terres contenant peu de fer cela est
souvent assez négligeable.
-
- Il peut être
intéressant de faire une ou plusieurs cuissons
à des températures intermédiaires
pour mieux décomposer la perte de masse du
produit.
- Par exemple : si la
température de fermeture de la glaçure
est connue, il peut être très instructif
de connaître la perte de masse avant et
après cette température, afin de pouvoir
mieux déterminer de la courbe de cuisson
(vitesse de montée, nécessité
dun palier de dégazage,
etc
).
-
-
- D) L'atmosphère de
cuisson doit être très oxydante
j'usqu'à 1000°C :
-
- La présence
d'oxygène dans l'enceinte du four par une bonne
aération est indispensable pendant toute la
montée en température jusqu'à
1000°C. Elle permet la combustion rapide des
minerais sulfurés et carbonés et une
décomposition plus précoce des
carbonates.
-
- Quelques exemples
:
-
- Combustion des produits
carbonés : En dessous de 1000°C, la
combustion du carbone ne produit que du gaz
carbonique, CO2. Le monoxyde de carbone CO ne pouvant
se former dans ces conditions de température.
En cas de manque d'air il subsistera donc du carbone
pur, on peut dans ces conditions avoir une
réaction du type suivant :
-
- 2C + O2 ==>
C + CO2
-
- Les composés
carbonés ayant une température
d'inflammation inférieure ou égale
à 700°C, Il faut veiller à une
bonne oxygénation des produits pendant la
montée à partir de cette
température. Dans le cas contraire du carbone
imbrûlé pourrait subsister et finir par
se combiner à l'oxygène des autres
matières par effet réducteur à
plus haute température bien après la
fusion de la glaçure, ce qui produirait des
bulles dans celle-ci.
-
- Décomposition de
la dolomie (carbonate de calcium et de
magnésium, CaMg(CO3)2) : La dolomie est un
carbonate double de calcium et de magnésium. Sa
décomposition varie selon l'atmosphère
de cuisson.
-
- Décomposition de
la dolomie dans l'air : La décomposition
commence vers 700°C.
- - Entre 700°C et
750°C elle est du type suivant : 2 CaMg(CO3)2
==> CaCO3 + CaO + 2MgO + 3CO2
- - Au delà de
750°C et jusqu'à 790°C elle permet
simultanément ces deux réactions :
- 1) CaMg(CO3)2 ==> CaO +
MgO + 2CO2
- 2) CaCO3 ==> CaO +
CO2
- à 790°C la
décomposition est terminée.
-
- Décomposition en
atmosphère saturée en CO2 (Cas de
présence de matières carbonées et
manque d'air) : La décomposition commence
à 550°C avec formation de CaCO3 et
MgO.
- - Entre 550°C et
765°C la réaction est la suivante :
CaMg(CO3)2 ==> CaCO3 + MgO + CO2
- - Au delà de
765°C et jusqu'à 910°C, la
réaction est stable, CaCO3 ne se
décompose pas.
- - De 910°C à
960°C CaCO3 se décompose en CaO et
CO2.
- à 960°C la
décomposition est terminée.
-
- Ici on mesure pleinement
l'influence de l'atmosphère du four sur la
décomposition de la dolomie. En présence
d'air la décomposition est terminée
à 790°C et en présence de gaz
carbonique elle s'achève seulement vers
960°C... D'où l'absolue
nécessité d'oxygéner le four lors
de la cuisson de pâtes dolomitiques, et encore
plus s'il y a présence de matières
carbonées.
-
-
-
-
-
- Combustion des minerais
sulfurés : La décomposition de la
grande majorité des minerais sulfurés
dans l'air est complète à partir de
900°C, en manque d'air elle est retardée
et se termine à plus haute température.
(ex : La Pyrite, sulfure de fer, se décompose
dans l'air à partir de 500°C. La
décomposition est entièrement
achevée à 800°C).
La réaction de
grillage dans l'air de la pyrite donne la
réaction suivante : 2FeS2 + 7O2 ==> Fe2O3 +
4SO2 . La combustion de la pyrite produit de l'oxyde
ferrique (Fe2O3) et du dioxyde de soufre (SO2) sous
forme de gaz.
- Le retard de cette
réaction entraine un dégagement gazeux
de SO2 à plus haute température avec
risque de bulles si la glaçure a
commencé à fondre.
- E) Le tesson sec doit
avoir une bonne cohésion et permettre
l'émaillage sans se rompre ou s'abîmer
sous l'effet de l'humidité.
Les pâtes peuvent
être améliorées par l'ajout de
dégraissants tels que chamotte et/ou silice,
ainsi elles supporteront mieux l'humidification due
à l'émaillage.
-
- Il est aussi possible
d'utiliser des glaçures à base de colles
et de liants organo-minéraux (Peptapon 9,
Déramite
) pour freiner la
pénétration de l'eau de la
glaçure dans le tesson cru sec. Il faut
privilégier l'émaillage sur tesson sec
plutôt que sur tesson vert (dureté cuir),
cela demande moins d'adjuvants pour faciliter le
recouvrement et donner de la cohésion à
la glaçure. Sur un tesson sec, la
porosité est importante et l'application d'une
glaçure encollée ou contenant des liants
organo-minéraux donnera les meilleurs
résultats.
-
- F) L'AIR DE RETRAIT des
pâtes pendant la vitrification : Un facteur
souvent oublié ou non pris en compte qui est
lié au fort retrait du tesson après la
fermeture de la glaçure.
-
- Ce défaut ne concerne
pas que la monocuisson, il peut toucher de même
les produits préalablement cuits en en
dégourdi de porcelaine ou en biscuit de
grès.
-
- Les pâtes à
fort retrait comme les grès et les porcelaines
ont des retraits linéaires compris entre 12 et
14 %. C'est à dire qu'un barreau cru mesurant
100 mm en longueur avant cuisson ne mesurera plus que
86 ou 88 mm après celle-ci.
-
- Si l'on considère ce
retrait en l'appliquant à un volume cubique
avec un cube ayant pour arête une dimension de
100 mm en cru, le volume sera de 100 x 100 x 100 =
1000000 mm3 soit 1 litre.
-
- Si la pâte a un
retrait de 14%, le cube après cuisson aura une
longueur d'arête de 86 mm et son volume sera de
86 x 86 x 86 = 636056 mm3 soit 0.63 litre.
-
- La différence entre
le volume cru et le volume cuit : 1 - 0.63 = 0.37
litre.
-
- Ce qui représente 37%
du volume initial et qui correspond à un volume
d'air expulsé lors du tassement du tesson sous
l'action de la vitrification. Pour ne pas
créer de malentendu sur la nature possible de
cet air, nous l'appelleront " air de retrait ".
Car lorsque la vitrification est quasi totale dans une
porcelaine bien cuite, la matière
céramique occupe plus de 99.5% du volume cuit
et on peut considérer que toute la
matière gazeuse contenue dans la
porosité initiale a été
expulsée.
-
- Par expérience, pour
ceux qui dégourdissent les porcelaines ou
biscuitent le grès avant émaillage, on
constate un très faible retrait pour ces
pâtes cuites autour de 980 à 1000°C.
En Général autour de 1%. Ceci signifie
que dans le cas d'une porcelaine mise en monocuisson,
à 1000°C elle aura encore à
expulser un volume d'air proche de ((37 / 14) * 13) =
34.3 % de son volume initial entre 1000°C et la
fin de sa cuisson. Si dans cet intervalle la fermeture
de la glaçure intervient précocement, il
pourra se produire des bulles dans celle-ci au moment
de l'expulsion de l'air de retrait s'il est
suffisament mis sous pression.
-
- Ce phénomène
est bien connu chez les potiers de grès qui
travaillent les glaçures mates au baryum
à cône 8 - 9. Si les pots sont
entièrement émaillés, ils
ressortent souvent criblés de cratères
après cuisson, malgré un bon biscuitage
et une atmosphère très oxydante. La
glaçure a emprisonné une bonne partie de
l'air de retrait bien trop tôt lors de la
montée en température, celui-ci ne peut
s'échapper librement et l'accroissement de la
température le dilate tout en diminuant le
volume du tesson qui le contient. Ce double effet
de dilatation de l'air et de la diminution de la
porosité du tesson accélère la
mise sous pression de ce gaz qui s'échappe en
formant des cratères dès que la force de
la pression peut vaincre la résistance de la
couche de glaçure fondue.
-
- Un remède n'est pas
toujours facile dans ce cas de figure, il faut soit
durcir la glaçure pour retarder son point de
fermeture tout en agissant sur l'allure de cuisson
(mais cela peut aussi nuire à l'effet de cette
glaçure), soit éviter un
émaillage intégral des pièces ou
encore avoir recours à une deuxième
glaçure durcie pour recouvrir les faces
secondaires des objets qui pourront laisser
s'échapper les gaz. Par exemple, un vase pourra
être émaillé normalement à
l'extérieur et non émaillé
intérieurement si le col est très
étroit et peut dissimuler cet artifice, ou bien
émailler l'intérieur du vase avec une
glaçure dure à point de fermeture
tardif.
- G) L'épaisseur des
pièces doit être régulière
pour que la maturité de cuisson soit uniforme
et que les plages de dégazage soient les plus
étroites possible (Une partie plus
épaisse mettra plus de temps à larguer
ses gaz).
-
-
- CONCLUSIONS / AVANTAGES
et INCONVÉNIENTS :
-
- Les avantages de la
monocuisson :
-
- L'économie
d'énergie
- Gain de temps au niveau des
manutentions du biscuit (enfournement,
défournement, stockage)
- Pas de risque de pollution
des biscuits stockés
- Économie de place
pour travailler
- Moins de stock
- Délai de production
plus court
- Visibilité plus
directe sur la qualité du travail
accompli
-
- Les inconvénients
de la monocuisson :
-
- Fragilité des
pièces avant cuisson, risque de casse lors des
manipulations
- Difficultés pour
désémailler sans abîmer le tesson
cru
- Retouches
difficiles
- Risque de bullage de la
glaçure ou de destruction du tesson en cas de
vitesse de cuisson inapropriée ou de
glaçure à fusion trop précoce,
etc...
- Un engobe alumineux sur les
plaques réfractaires est indispensable pour
éviter les problèmes de
collage.
-
-
-
-
-
-
-
-
- Smart2000.fr
©
Juin 2009 - Nov
2023
-
FRANCE
- Écrit
et documenté par le propriétaire du site
// Contact : Smart2000@wanadoo.fr
- Document
pour CONSULTATION PRIVÉE uniquement
- Toute
reproduction totale ou partielle est
interdite
-
-
-
-
- Smart2000.fr
le site
dédié aux passionnés de
céramique
-
- Smart2000
- FRANCE sur https://smart2000.fr/
-
- This
entire page Copyright © 2009-2023, All Rights
Reserved.
- Les
textes et les photos restent la
propriété de leur auteurs, ils ne
peuvent être réutilisés sans un
accord préalable. Nous
consulter.
|