- Sommaire
-
- Sur cette page :
Classification des Céramiques
présentées à l'exposition des
produits de l'industrie Nationale en 1834 à
Paris, dont :
-
- introduction----------------les
genres de poteries
-
- la
terre cuite----------------la
poterie commune
-
- la
faïence commune----------------la
faïence fine
-
- poterie
de gres----------------la
porcelaine
-
- la
porcelaine dure----------------la
porcelaine tendre
-
- le
pyromètre de Wedgwood----------------l'échelle
de pouillet
-
- Exposition
de 1834, Classification des Produits de
l'Industrie Céramique
- par
Smart2000
|
-
-
-
-
- Extraits d'un
rapport sur l'Exposition des Produits de l'Industrie
Nationale de 1834 concernant la Céramique
:
-
- Il s'agit d'une étude
de classification des produits céramiques
présents sur le marché de cette
époque faite dans le but de renseigner le
consommateur. Le texte est reproduit
intégralement tel que transmis par son auteur,
Stéphane Flachat, dans son étude de
l'industrie parue à l'occasion de l'exposition
de 1834.
- Outre le côté
verbeux et très détaillé du
français de cette époque, on y retrouve
l'essentiel des connaissances céramiques du
moment dont la plupart des valeurs demeurent
inchangées en ce début de 21ème
siècle.
-
- Introduction
:
-
- " Une classification des
divers genres de poterie est indispensable. Au milieu
de tant de produits d'apparence si semblable, de
qualité si différente en
réalité, dont les magasins de vente
offrent journellement au consommateur l'embarrassant
assemblage, et qu'il retrouve à l'exposition ;
dans ce dédale de dénominations
menteuses inventées par la spéculation,
sous ces vernis brillants, sous ces peintures, qui
trop souvent encore cachent des terres mal
préparées et mal cuites, quel moyen le
consommateur a-t-il de vérifier la
qualité réelle de l'objet qu'il
achète ? Un seul, l'usage, expérience
coûteuse, même quand il a
été induit à la faire par le bon
marché. C'est surtout en matière de
consommations habituelles que ce genre d'appât
est ruineux "
-
- Les
céramiques :
-
- " Les deux principes
constituants de toutes les poteries sont la silice et
l'alumine (1). Les argiles pures et les kaolins sont
particulièrement composés de ces deux
terres, et offrent par conséquent les
matériaux les plus habituels pour la
fabrication des poteries fines et des porcelaines. Les
argiles figulines (Lat. figulus, potier) et des
marnes argileuses qui sont composées d'argile
et de craie (silice, alumine, carbonate de chaux),
sont d'un usage général et
économique pour les faïences et poteries
communes.
- Il paraît
démontré que la bonne qualité des
pâtes dépend surtout des proportions de
leurs principes constituants, et que mieux la
combinaison chimique de ces principes est
opérée, plus les produits qu'elles
donnent réunissent eux-mêmes des diverses
qualités qu'on y recherche "
-
- (1) Dans quelques
fabrications d'Italie et d'Espagne, on emploie des
terres où la magnésie tient lieu
d'alumine. On appelle ces terres " giobertite " et "
magnésite ".
-
- " La combinaison chimique et
à proportion définie de la silice et de
l'alumine forme, en langage chimique, un silicate
d'alumine. La faïence fine d'Angleterre par
exemple, dont la pâte est si dense et si
homogène, paraît composée de
silice et d'alumine en proportions telles qu'elles se
neutralisent plus complètement que dans les
faïences françaises ; en d'autres termes,
la quantité de silice ou d'alumine qui y reste
libre de combinaison chimique paraît y
être moins forte que dans les autres poteries,
qui sont aussi des silicates d'alumine, mais avec plus
de silice ou d'alumine non neutralisée
"
- " Cette combinaison plus
intime, plus chimique des pâtes, résulte
des procédés de fabrication autant que
des proportions constitutives des matériaux
employés. "
-
- Les divers genres de
poteries :
-
- M. Brongniart
établit, et nous croyons qu'on peut admettre
avec lui, sept sortes de poteries :
-
- - les terres
cuites,
- - la poterie
commune,
- - la faïence
commune,
- - la faïence
fine,
- - la poterie de
grès,
- - la porcelaine
dure,
- - la porcelaine
tendre.
-
- Les terres
cuites :
-
- " Nous n'avons pas ici
à nous occuper de la première classe,
qui comprend les briques, tuiles, carreaux, fourneaux,
réchauds, tuyaux de conduite, statues de jardin
ou de poêles. Ces divers produits,
composés d'argile figuline, ou de marne peu
travaillée, et mêlée de sable ou
de débris de terre cuite, constituent ,
quelques-uns du moins, des produits importants, dont
la fabrication déjà perfectionnée
doit, sans aucun doute, recevoir plus
d'amélioration encore, mais n'entrent pas dans
le sujet que nous traitons ici. "
-
- La poterie
commune :
-
- " La poterie commune,
Assiettes, terrines, marmites, avec vernis jaune, vert
ou brun, est employée soit comme vaisselle dans
les pauvres ménages, en raison de la
modicité du prix, soit pour les usages
domestiques, et notamment pour ceux de la cuisine, par
les classes aisées qui n'ont rien encore
à y substituer. Cette poterie va au feu,
voilà son avantage, et l'on n'a pas
déterminé précisément
à quelle cause on peut l'attribuer.
- Quoi qu'il en soit, ces
poteries, celles, par exemple, qui se fabriquent dans
les environs de Paris, sont composées d'argiles
plastiques brunes, extraites à Gentilly,
Arcueil, Vaugirard, et de sable siliceux contenant un
peu de marne ferrugineuse et qui se trouve aussi au
environs de Paris.
- L'argile plastique prend
cette dénomination, non de ses
propriétés ou proportions chimiques,
mais d'une qualité physique, celle de former
une pâte liante, et conservant les empreintes
que la main de l'ouvrier donne. La pâte de
poterie est longue ou courte, suivant
que la plasticité de l'argile est plus ou moins
développée.
- Toutefois, comme l'argile
seule ne présente pas assez de fermeté,
et qu'après avoir été
ébauchée ou préparée au
tour à potier, elle se déformerait par
la dessiccation ou la cuisson, on la mélange
toujours d'une matière qu'on appelle
dégraissante ; tantôt c'est du
sable, tantôt de la craie, tantôt du
ciment de pâte analogue et
broyée.
- Dans le poterie dont nous
nous occupons, le sable siliceux forme la
matière dégraissante ; il entre pour un
cinquième dans la pâte. L'argile et le
sable sont mêlés par le marchage ; on y
ajoute des rognures de pâte déjà
maniée, et la pâte est
fabriquée.
- Toutes les pièces
rondes sont façonnée par
ébauchage. L'ébauchage est la
façon qui consiste à donner à la
pâte molle une forme quelconque avec les mains,
et sans moule. Cette opération se pratique au
tour à potier.
- Les autres pièces se
façonnent à la main, ou quelquefois dans
des moules en plâtre.
- Ainsi
préparées, elles sont portées au
four pour être cuites, ou, en termes d'art, pour
être biscuitées.
- Il reste à les
vernisser, opération indispensable, et sans
laquelle ces poteries ne pourraient tenir l'eau, ni
servir à aucun des usages auxquels on les
applique. Le vernis jaune est composé, pour 100
parties, de 64 de minium ou litharge (oxyde de plomb,
PbO), argile 16, sable 14. Cette combinaison produit,
exposée au feu, une substance qui se
liquéfie et prend l'aspect vitreux. Ces
matières sont broyées sous une meule, et
forment avec de l'eau une bouillie, dont on asperge la
partie des pièces qu'on veut vernisser. Elle
est alors ainsi reportée au four, où une
chaleur bien moins considérable que celle de la
cuisson, fait fondre le vernis, et donne à la
poterie l'aspect que nous lui connaissons.
- Quand on veut un vernis
brun, on ajoute du manganèse à la
composition indiquée plus haut, et on en
ôte un peu de minium ; quand on veut un vernis
vert, on l'obtient par l'addition d'un peu de
protoxyde de cuivre.
- Il existe une poterie
commune d'un genre un peu différent ; elle a un
fond jaune, avec des taches d'un violet pâle.
Elle est faite à Épernay. L'argile
plastique avec laquelle on la prépare est
blanche, et conserve cette couleur à la
cuisson. La fermeté de cette pâte permet
que les pièces soient vernissées crues.
On leur donne d'abord un enduit terreux et fusible,
appelé engobe ; puis on met une couche
de minium par aspersion, et on projette dessus de
l'oxyde de manganèse. Ainsi se produit cette
apparence mouchetée de la poterie
d'Épernay ; cette poterie ne présente
pas d'autres différences avec celle de
Paris.
- A Magnac-Laval
(Haute-Vienne), on fabrique une poterie analogue, et
qui est d'un noir brillant obtenu sans avoir recours
à l'opération du vernissage. Cette
poterie cependant, particulièrement
destinée aux lessives, peut en contenir de
bouillante sans transsudation. Pour lui donner cette
couleur noire, on met en pratique le
procédé suivant : on introduit dans le
four du bois humide au moment où la cuisson de
la poterie s'achève ; il s'y développe
ainsi une grande quantité de fumée
chargé de charbon en poussière
ténue ; pour que cette fumée
séjourne dans le four, et s'imprègne
bien dans la pâte, on ferme toutes les issues du
four ; la poterie sort d'un noir mat ; on lui donne le
brillant en la frottant avec du foin.
- Tels sont les
procédés généraux de
fabrication de la poterie commune. C'est celle dont la
pâte subit le moins de préparation, la
cuisson la moins forte, et qui reçoit le vernis
le plus facilement fusible. C'est en un mot, celle qui
réunit toutes les conditions du bon
marché. Mais, à cause de cela
même, elle est d'un mauvais usage. La pâte
et le vernis n'offrent aucune solidité. Cette
poterie va au feu, mais elle s'y écaille ou
fendille facilement ; une fois le vernis
entamé, les matières liquides et grasses
pénètrent le corps de la poterie, et
bientôt y déposent une odeur qu'aucun
lavage, qu'aucun soin ne peuvent enlever. Le vernis
d'ailleurs, presque entièrement composé
de plomb, est insalubre, et peut se mêler aux
aliments toutes les fois qu'ils ont reçu une
cuisson un peu forte dans des vases de ce
genre.
- " On a, dit M. Brongniart,
cherché à perfectionner cette poterie en
lui donnant un tissu plus serré et un vernis
purement terreux, et cependant aussi fusible que le
vernis plombifère. C'est à M. Fourmy
qu'on doit les recherches et les tentatives
d'exécution de cette sorte de poterie ; mais il
parait qu'on n'a pas encore pu réussir à
introduire ce genre de perfectionnement dans la
fabrication en grand, usuelle et économique, ni
pu atteindre le prix si bas de la poterie commune
à vernis plombifère ; or, le prix est la
qualité que le peuple, grand consommateur de
cette sorte de poterie, prise au dessus de tout ; et
comme malheureusement il n'est pas convaincu du danger
de la poterie plombifère, il lui donne toujours
la préférence, même à prix
égal, sur la poterie salubre, parce que cette
dernière n'offre pas les couleurs brillantes,
le vernis luisant qui frappe les yeux, et attire le
choix des personnes dont les sens sont, en
général, mus, même dans les plus
petites choses, que par des qualités et des
propriétés tranchées.
"
- Il y a une conclusion
à tirer de réflexions si sensées
; nous le ferons plus loin.
-
-
-
-
- La
faïence commune :
-
- " La faïence commune
est de deux sortes : la faïence blanche et la
faïence brune. Il n'y a pas de différence
sensible dans leur procédés de
fabrication, mais il y en a dans leurs matières
premières, et cette différence est assez
notable pour en amener une fort grande dans leurs
usages économiques. La première ne
soufre pas le feu, et la seconde le supporte avec une
grande sûreté.
- Les pâtes de ces deux
faïences sont composées d'argile
d'Arcueil, de marne argileuse verdâtre, de marne
calcaire blanche et de sable marneux. Toutes ces
terres se trouvent dans les environs de Paris, dans le
voisinage les unes des autres. En langage
géognostique, elles font partie des formations
supérieures du terrain tertiaire sur lequel
repose Paris. On croit que la différence de
qualité ou d'usage qui existe entre les deux
faïences tient à ce que, dans la
pâte de faïence brune, la marne blanche est
en plus petite proportion que dans la faïence
blanche, à laquelle elle donne plus
d'éclat, plus de sonorité, mais qu'elle
rend impropre à supporter le feu.
- La principale
différence qui existe entre les
procédés de fabrication de la
faïence commune et ceux de la poterie commune,
consiste en ce que pour ce genre de faïence les
pâtes sont travaillées avec plus de soin,
les matières sont choisies plus ténues,
moins mêlées de parties
étrangères, dont on les dégage
d'ailleurs (principalement l'argile) par le lavage. La
pâte gâchée n'est pas
employées immédiatement, mais est
conduite en bouillie dans des fosses, où on la
laisse exposée à l'air, la pratique
ayant prouvé qu'elle s'y améliorait. Il
paraît que, pendant ce repos accordé
à la pâte, l'action chimique commence
à s'y exercer, et, en la rendant plus
homogène, lui donne quelques premières
traces des qualités les plus recherchées
pour l'emploi qui doit en être fait.
- Lorsque la pâte est
ainsi préparée, bien battue et
corroyée, on prépare les pièces,
soit par le procédé d'ébauchage
(tournage), et qui s'emploie plus
particulièrement pour faire la faïence
brune, soit par le procédé dit de
tournassage, qui produit des pièces plus
légères et de formes mieux
déterminées, ce que l'on recherche
particulièrement dans la fabrication de la
faïence blanche.
- L'opération de
tournassage consiste à repasser sur le tour la
pièce qui déjà y a passé
pour l'ébauchage. Mais alors la pâte
n'est plus assez molle pour que la main
désarmée de tout instrument puisse y
imprimer une forme. Elle est déjà au
contraire à un état de dessiccation
assez grand pour supporter l'attaque d'outils en fer,
et toutefois assez humide encore pour ne pas
s'égrener à leur contact et s'enlever au
contraire en copeaux. L'opération du
tournassage s'effectue donc, comme celle de
l'ébauchage, au tour de potier, mais avec un
moyen d'action plus pénétrant et qui
permet d'obtenir des formes plus
régulières et plus fines.
- Quant aux pièces
plates, rondes, telles qu'assiettes, elles se font
dans des moules de plâtre, et par moulage
à la croûte. Ce moulage consiste
à faire avec la pâte sur une table une
lame ou une croûte d'une épaisseur
calculée sur celle qu'on veut donner au objets
à mouler. On applique ensuite cette
croûte sur les moules ; pour la faïence
commune, la croûte se prépare en battant
la pâte avec un tampon de plâtre dur
constamment tenu humide.
- Portées ensuite au
four, les pièces y subissent une cuisson de
trente-six heures, plus longue par conséquent
que celle de la poterie commune.
- Puis, on émaille les
pièces et on le remet au four, où on
leur fait subir une chaleur au moins égale
à celle de la première opération.
On n'a pas pu réussir encore à mettre
l'émail sur la pièce crue ; sans cela on
pourrait n'avoir qu'une cuisson, puisque le vernis et
la pâte subissent une égale
température.
- Tandis que dans la poterie
commune l'émail ou vernis est translucide, dans
la faïence commune, il est opaque, et dissimule
par conséquent la texture de la pâte.
Pour la faïence brune, c'est une terre qui donne
cette opacité ; pour la faïence blanche,
c'est de l'oxyde d'étain. L'émail brun
se compose de minium, de manganèse, et de
poudre de brique fusible ; l'émail blanc se
compose d'oxyde d'étain, d'oxyde de plomb, de
sable quartzeux, de sel marin ou de soude. On colore,
si l'on veut, l'émail blanc en jaune avec
l'oxyde d'antimoine ; en bleu, avec de l'oxyde de
cobalt à l'état d'azur ; en vert pur,
avec du protoxyde de cuivre et du jaune de Naples ; en
émail violet, avec du peroxyde de
manganèse.
- Tels sont les
procédés sommaires d'une des branches
les plus importantes de l'art de la poterie. La
faïence commune est employée par de
nombreux consommateurs, soit parce qu'elle est
déjà d'une couleur et d'une forme assez
agréables pour ne pas déparer les
ménages modestes, soit parce qu'elle est
vraiment propre à des usages nombreux de
cuisine, pour lesquels les fortunes médiocres
n'ont rien a y substituer dans l'état actuel
des choses. Toutefois, l'agrément de couleur de
la faïence blanche ne tenant qu'à son
vernis opaque, cet agrément est de peu de
durée, car ce vernis se fendille,
s'écaille, en termes techniques, tressaille
facilement. Alors la pâte mise à
découvert fait sur la pièce une tache
irrémédiable, et bientôt l'odeur
des corps gras la met hors de service. C'est un grave
inconvénient de cette faïence.
-
- La
Faïence fine :
-
- Les caractères
généraux de la faïence fine
sont établis par M. Brongniart avec la plus
parfaite lucidité.
- Cette poterie est
caractérisée par une pâte blanche,
opaque, à texture fine, dense et sonore,
recouverte d'un vernis de plomb et
cristallin.
- La pâte est
essentiellement composé d'argile plastique
lavée, et de silex broyé fin. Il y a
quelquefois un peu de craie ; cette pâte est
très fine et très plastique.
- L'enduit est un vernis
cristallin, fondu préalablement en verre, et
composé de silice unie à du quartz ou
même à du feldspath, de soude, et de
plomb à l'état de minium.
- Ce verre,
délayé dans l'eau à l'état
de bouillie épaisse, est mis par immersion ou
par arrosage sur les pièces, après
qu'elles ont subi une première cuisson dont la
chaleur est très forte. Celle qui est
nécessaire pour le vernis est de beaucoup
inférieure.
- Cette poterie est
susceptible de recevoir des décorations
très variée, en fond de couleur, lustre
métallique, ornements et peintures par voie
d'impression. Comme elle est principalement
employée par des personnes d'une aisance
moyenne, les décorations soignées en
sont assez appréciées, et comme elle est
très répandue, les pièces de
même sorte et de même décoration
peuvent être assez multipliées pour que
le débit couvre les frais de premier
établissement, que nécessitent les
moyens mécaniques de
décoration.
- La couleur blanche ou
déterminée qu'on peut donner à la
pâte de cette poterie, l'éclat et la
solidité de son vernis, et surtout la finesse,
la légèreté, la pureté du
contour que peuvent offrir ses pièces, sont des
qualités qui la font rechercher. D'un autre
coté, la plasticité de sa pâte qui
en rend le travail facile, expéditif et
sûr, les moyens mécaniques et les
procédés économiques qu'on peut
mettre en usage pour rendre cette fabrication encore
plus expéditive, permettent de réduire
considérablement le prix de cette poterie, sans
que ce soit ni aux dépens de ses
qualités fondamentales, ni même aux
dépens de ses qualités accessoires qui
tiennent au goût, à la pureté des
formes et des décorations. Cette
réduction de prix, en étendant
considérablement le débit et la
fabrication, permet une nouvelle économie dans
la production et dans la vente pour les pays où
cette fabrication est conduite en grand et avec une
longue expérience.
- Les défauts de cette
poterie qui tiennent à sa nature sont de ne
pouvoir aller sur le feu pour les usages domestiques,
et d'avoir un vernis tendre qui se laisse facilement
entamer par les instruments d'acier et de fer. Mais,
lorsque cette poterie est mal fabriquée ou
fabriquée avec une économie mal
entendue, ses défauts deviennent bien plus
graves ; son vernis jaunâtre et tendre
tressaille souvent ; il se laisse entamer ou user avec
une grande facilité par les instruments de fer
ou par l'usage ordinaire. Les fissures que ce
tressaillement ou ces rayures ouvrent dans le vernis
permettent aux matières grasses de
pénétrer dans le biscuit qui, dans les
poteries affectées par ce défaut, a
presque toujours une nature lâche ; les
pièces se salissent, s'empuantissent, et se
brisent même facilement.
- Il est important de
reconnaître ces défauts, qui ne se
manifestent pas au premier aspect. Il y a plusieurs
moyens, qui sont presque à la portée de
tout le monde.
- 1° . Le vernis se
laisse entamer facilement au couteau.
- 2° . Les pièces
de cette poterie, placées dans un lieu
où se dégagent des odeurs de
matières putrides, ne tarderont pas à se
couvrir de couleurs irisées, et même de
se noircir.
- 3° . Un uf
mêlé d'un peu de graisse et cuit sur une
pièce rayée, fera naître à
sa place une couleur irisée ou d'un brun
noirâtre, qui s'étendra à une plus
ou moins grande distance de la rayure, suivant la
mauvaise qualité du vernis ou du
biscuit.
-
- On distingue deux genres
dans la faïence fine, le cailloutage en terre
anglaise et la terre de pipe.
- Le cailloutage en terre
anglaise, ainsi appelé parce que la
matière dégraissante ne consiste qu'en
silex broyé, est l'objet d'une immense
fabrication en Angleterre où ses produits se
livrent à très bas prix. Cette
faïence est imitée en France, dans les
grandes fabriques de Creil, Montereau, Choisy,
Chantilly, dont nous voyons les produits à
l'exposition.
- Des différences
notables existent entre les procédés
anglais et français.
- Une des plus importante,
c'est celle de la matière première ;
l'argile plastique du Devonshire et celle du
Dorsetshire sont bien plus riches en alumine que les
argiles de Montereau, par conséquent plus
plastiques et d'un maniement beaucoup plus
économique. L'argile de Montereau contient
d'ailleurs un peu de fer, et lorsqu'on veut lui faire
subir une température semblable à celle
que les Anglais donnent à leur faïence
fine, elle prend une teinte rougeâtre, provenant
de la coloration par l'oxyde de fer.
- La composition des
faïences fines du Devonshire et du Dorsetshire
paraît être, sur 100 parties, de 62
d'argile plastique, 16 de kaolin de Cornouailles, 19
de silex, 3 de feldspath en partie
décomposé.
- Le plus grand soin est
apporté dans la préparation de la
pâte. Pour que le mélange ait lieu de la
manière la plus intime, après que les
argiles ont été lavées, et le
silex trituré très fin, on en fait une
bouillie claire, appelée barbotine, que
l'on gâche longtemps. La barbotine est
amenée ensuite dans des caisses qui, dans
quelques fabriques anglaises, ont jusqu'à 60
pieds de long. Ces caisses faites de plaque de terre
cuite sont entourées ensuite de combustible
pour faire évaporer en partie l'eau de la
pâte ; puis cette pâte est reprise et
portée dans des moulins, où des machines
d'une grande force la pétrissent dans des
cylindres de fonte, et en dégagent tout l'air
interposé. La pâte, après cette
opération, reste encore plusieurs mois dans des
caves humides.
- Cette pâte est alors
d'un usage si convenable pour la fabrication, qu'on
assure qu'un ouvrier anglais, assisté de deux
apprentis qui lui apportent les balles de pâte,
et qui emportent la pièce
ébauchée, peut ébaucher une
assiette en huit ou dix secondes, par
conséquent, 3600 dans sa journée de dix
heures.
- Dans cette fabrication, le
moulage a généralement lieu à
la croûte ; nous l'avons décrit plus
haut. Les pièces ébauchées sont
finies par le tournassage.
- La cuisson a lieu à
la houille ; elle s'opère en 15 heures ; plus
rapidement, par conséquent, que celle de la
faïence commune : toutefois la chaleur
développée est bien plus forte que pour
la cuisson de cette faïence. Le vernis dont nous
avons fait connaître tout à l'heure les
principes constituants est mis sur les pièces
cuites, et n'a besoin, pour son application, que d'une
chaleur évaluée au tiers seulement de
celle qu'exige la cuisson du biscuit.
- Quant aux
procédés des fabriques
françaises, la différence que nous avons
signalée dans les matières
premières employées en amène
quelques-unes dans le reste de la fabrication. Les
principales consistent en ce que la cuisson est moins
forte, et que la pâte étant moins dense,
il faut varier un peu la composition du vernis, qui
est moins dur aussi que le vernis anglais.
- Parmi les fabriques
françaises, il en est quelques-unes toutefois
qui se rapprochent de la pâte et des vernis
anglais. Nous les signalerons plus loin.
- Les principaux
défauts de la faïence fine résident
dans son vernis qui est tendre, altérable et
susceptible de tressaillir. On a imaginé de
couvrir un biscuit analogue par sa composition
à celui de cette faïence, avec
l'émail opaque stannifère et très
dur de la faïence commune. C'est ce que l'on
appelle terre de pipe.
- Cette poterie peut avoir les
formes délicates et la
légèreté de la faïence fine,
en même temps que l'émail glacé,
bien blanc et dur, de la faïence commune. Mais
cet émail épais et opaque alourdit un
peu les formes. La principale objection contre ce
genre de faïence, c'est qu'elle est d'un prix
trop voisin de celui de la porcelaine, pour qu'on lui
donne la préférence sur
celle-ci.
-
-
-
-
-
- Poterie de
grès :
-
- La poterie de
grès prend son nom plus encore de son
aspect physique, que des proportions chimiques de sa
pâte. Il faut la distinguer en poterie commune
et poterie fine.
- Dans la poterie de
grès commune, la pâte est d'argile
plastique siliceuse, à laquelle on ajoute un
peu de sable. Cette argile n'est pas lavée,
mais seulement épluchée ; elle est
marchée et pétrie avec soin : sa couleur
est grisâtre. Le point saillant de cette
fabrication, c'est la longueur de la cuisson ;
à Saveignies, près de Beauvais, elle
dure huit jours ; quatre jours dans le voisinage de
Briare. A Saveignies et en Bretagne on ne donne pas de
vernis à cette poterie, qui n'en est pas moins
imperméable au liquides. A Briare, on l'enduit
d'un vernis particulier, du genre des couvertes, et
faite avec le laitier des fourneaux à fer. Le
vernis est mis sur le cru ; la pâte et la
couverte cuisent ensemble ; celle-ci prend une couleur
marron, est unie, brillante et très dure. A
Sartpoterie, dans le département du nord, on
fait une poterie qui tient au genre que nous examinons
; elle est d'un gris de lin assez agréable,
d'une fabrication un peu plus soignée, et
souvent ornée de dessins, taches et
linéaments, faits avec une couverte
bleuâtre, dont la couleur est due à
l'oxyde de cobalt.
- Souvent ces poteries ont un
vernis très fins et translucide : il est obtenu
par un procédé aussi simple
qu'économique, et qui consiste à
projeter du sel marin dans le four, au moment
où la cuisson se termine. Ce sel se volatilise,
et vient former un fondant à la surface des
pièces cuites, où il se
décompose, et laisse son alcali.
- Les grès anglais,
fabriqués à Londres, sont cuits à
la houille presque jusqu'à la fin de
l'opération, où l'on introduit dans le
four du bois, dont la cendre alcaline
volatilisée donne à ces grès
l'enduit vitreux qu'ils présentent.
- La fabrication de ce genre
de poteries est aussi très avancée en
Allemagne ; la pâte en est fine et les ornements
soignés ; leur couleur est le brun-marron et le
gris-foncé : ils sont recouverts d'un enduits
vitreux mince, dû à la volatilisation du
sel marin. Ils sont, en outre, ornés, comme les
vases de Cologne, de parties émaillées
avec une couverte colorée en bleu par le
cobalt.
- La poterie de grès
fine, particulièrement fabriquée en
Angleterre paraît se composer d'un quart
d'argile plastique blanche, d'un quart de kaolin,
d'une moitié de feldspath ; il en
résulte une pâte qui a une assez grande
fusibilité, qui peut se passer de vernis ou de
couverte, ou n'en reçoit pas d'autre que celui
qui provient de la volatilisation des parties
alcalines des terres qui composent les enveloppes dans
lesquelles ces pièces de poterie sont cuites.
Cette poterie est susceptible de recevoir des
ornements très fins et très
brillants.
- La Chine et le Japon
fabriquent cette sorte de poterie avec une grande
habileté.
- Les grès anglais
faits maintenant dans toutes les fabriques de
faïence fines, concurremment avec ces
faïences, parce qu'ils remplissent dans le four
des places où ils cuisent mieux que ne le
ferait la faïence, sont extrêmement
remarquables par la variété de leur
couleur, la finesse de leur pâte, la richesse et
la pureté de leurs godrons et ornements. C'est
au célèbre Wedgwood qu'on doit cette
jolie poterie.
- La fabrique française
de Sarreguemines, dirigée par MM. Fabry et
Utschneider, a, dans ce genre, des produits
extrêmement remarquables.
-
- La
Porcelaine :
-
- On en distingue de deux
sortes, la porcelaine dure et la porcelaine
tendre.
- Ce qui distingue
particulièrement la porcelaine de la
faïence, c'est que contenant dans sa pâte
même un alcali, la potasse, qui est un des
éléments du feldspath,
élément essentiel lui-même de la
porcelaine, elle participe des corps vitreux. La
translucidité de la pâte tient à
cette circonstance de sa composition. Ses principales
qualités en dérivent aussi.
- Ce qui différentie la
porcelaine tendre de la porcelaine dure, c'est que
cette dernière contient une moins grande
quantité d'alcali, et, par conséquent,
est moins vitreuse ; elle a d'ailleurs pour enduit
vitreux une couverte terreuse dure, qui ne fond
qu'à haute température ; la porcelaine
tendre a un vernis vitreux, transparent, tendre,
plombifère.
- La pâte de l'une et de
l'autre est essentiellement composée de deux
éléments principaux ; l'un, argileux,
infusible, donné ou par le kaolin ou par
l'argile plastique pure et blanche ; l'autre, aride et
fusible, est donné par le feldspath, auquel on
ajoute parfois du sable siliceux, de la craie,
etc.
-
- La
Porcelaine dure :
-
- La couverte de la porcelaine
dure consiste en feldspath, tantôt seul,
tantôt mêlé avec du
gypse.
- La pâte de la
porcelaine dure demande plus de soin que celle
d'aucune autre poterie. Les matériaux en
veulent être mieux choisis, mieux lavés,
mieux broyés, mieux mélangés, la
pâte mieux pétrie et plus maniée.
Toutefois, elle est toujours courte, ce qui en rend le
façonnage assez lent.
- Les autres
procédés de fabrication doivent
être également plus soignés de
tout point. L'art arrive ici à ses plus grandes
difficultés comme à ses plus
délicats chefs-d'uvre.
- La cuisson est simple. Les
pièces éprouvent un premier feu, mais
c'est pour en dégager complètement
l'humidité ; ayant acquis ainsi la
fermeté nécessaire, on leur donne la
couverte par immersion. On les cuit alors, et la
pâte et la couverte subissent la même
température, la plus forte des arts de la
poterie. On l'évalue à 140 degrés
du pyromètre de Wedgwood (*) ; c'est une
température environ cent fois plus forte que
celle de l'eau bouillante (ceci est une image.. la
température réelle ne devait pas
dépasser 1400 à 1450°C, mais
à cette époque aucune corrélation
de niveau thermique ne permettait de relier
l'échelle Celsius basée sur
l'état liquide de l'eau et les hautes
températures des fours céramiques
exprimées en degrés sur le
pyromètre de Wedgwood).
-
-
- (*)
PYROMETRE DE WEDGWOOD : Du
nom de Josias Wedgwood, fabricant de porcelaines
anglais, qui construisit cet instrument en 1782 pour
permettre d'apprécier la température des
fours céramiques.
- Ce fut le premier
instrument permettant une mesure précise de la
température des fours. Il est basé sur
le fait que lorsqu'un cylindre d'argile est
porté à haute température pour le
cuire, il prend un retrait proportionnel à la
température atteinte. En employant toujours la
même argile, façonnée toujours de
la même façon, Wedgwood obtenait des
éprouvettes en forme de demi-cylindres
identiques terminés par une partie plate. Ces
éprouvettes étaient chauffées
préalablement au rouge sombre (ce qui
correspond environ à 600°C et au
départ de l'eau de cristallisation de la
kaolinite) ; après refroidissement, elles
étaient disposées dans les fours dont on
voulait observer la marche des températures et
de telle façon qu'il était possible de
les retirer en cours de cuisson à l'aide d'une
tringle de fer passant par un couloir dit " trou de
montre " .
- A cette époque on
ne savait traduire les hautes valeurs de
température sur aucune échelle de
mesure, aussi pendant plus d'un siècle
l'échelle de Wedgwood servira de
référence pour déterminer les
niveaux de cuisson atteints dans les fours
céramiques. Et c'est bien plus tard, suite aux
travaux de Henry Le Châtelier (inventeur du
thermocouple en platine-platine rhodié en 1886
permettant pour la première fois de mesurer des
températures allant jusqu'à plus de
1700°C) et de M. Boudouard, qu'une
corrélation sera faite avec l'échelle
Celsius** étendue (Voir graphique
ci-après).
-
-
-
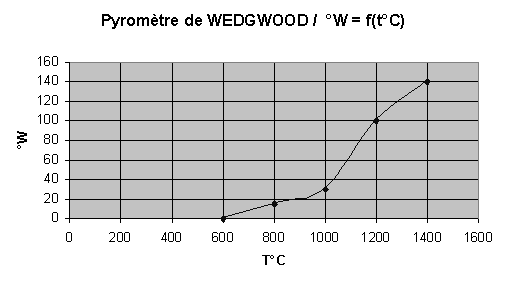
-
-
-
-
- Le pyromètre de
Wedgwood se compose de deux plaques de laiton
appelées jauges. Chacune étant
formée par deux règles
métalliques à parois inclinées et
dont les arêtes supérieures internes sont
convergentes et graduées à l'aide de
divisions égales ; la première jauge, de
0 à 120 ; la deuxième jauge, de 120
à 240.
- Le zéro de
l'appareil correspond au diamètre des
éprouvettes portée à 600°C
environ (la couleur "rouge sombre " du four servant de
repère pour ce traitement thermique). La
réduction de diamètre due à la
cuisson permettait de faire coulisser
l'éprouvette dans la jauge jusqu'à ce
qu'elle se coince entre les deux règles. Il
suffisait alors de lire la graduation portée en
face de l'extrémité plate de
l'éprouvette pour évaluer son
degré de cuisson.
-
-
-
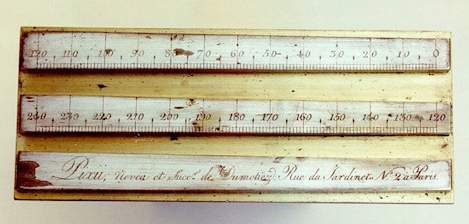
- Pyromètre de
Wedgwood
-
-
- ** : Anders Celsius
(Né en 1701 à Uppsala en Suède)
élabore en 1742 un thermomètre à
mercure basé sur une échelle
centésimale des températures et dont le
0 marque le point d'ébullition et 100 le point
de congélation de l'eau. Cette échelle,
l'une des premières du genre, sera
inversée après la disparition de son
inventeur (en avril 1744), adoptant sa forme
actuelle.
-
- Avant cette invention,
dans la plupart des ateliers de céramique et en
particulier dans les porcelaineries, on utilisait
généralement l'échelle de
Pouillet, basée sur la perception des nuances
de rouge du four :
-
- Échelle de
Pouillet :
-
- (appréciation de
la température par l'il en fonction de la
couleur dans le four)
-
- Rouge naissant
525°C
- Rouge sombre
700°C
- Rouge cerise naissant
800°C
- Rouge cerise proprement
dit 900°C
- Rouge cerise clair
1000°C
- Rouge orange foncé
1100°C *
- Rouge orange clair
1200°C
- Rouge blanc
1300°C
- Rouge blanc soudant
1400°C
- Rouge blanc
éblouissant 1500°C
-
- (*) : A partir du rouge
orange foncé, il faut se protéger en
utilisant des verres colorés pour filtrer le
rayonnement (Verres au cobalt ou teintés en
vert).
-
- Ces appréciation
visuelles sont nettement fonction de
l'observateur.
-
- Un observateur
entraîné (enfourneur) arrive à
pouvoir affirmer, par exemple, qu'un alandier est plus
chaud qu'un autre, que le four est en avance ou en
retard par rapport au nombre d'heures
écoulées depuis
l'allumage.
- Ce moyen était le
plus utilisé dans les porcelaineries
françaises à la fin du 19ème
siècle et même encore dans une bonne
partie d'entre elles avant la seconde guerre mondiale.
Autant dire que les résultats de cuisson de
cette époque étaient totalement
dépendants de la " mémoire " visuelle du
chauffeur de four, car rien n'est plus difficile a
distinguer que les nuances du feu lorsqu'il n'y a rien
à mettre en comparaison excepté l'intime
conviction de reconnaître avoir atteint un
niveau de couleur dont on est sûr
à
plusieurs dizaine de degrés près, et
parfois
plus.
-
- Références
:
- Fabrication
Industrielle des Porcelaines, Cuisson -
Décoration, Tome 2, par Marc Larchevêque
- 1929
-
- A cette température
la pâte se ramollit, ce qui exige de grandes
précautions dans les procédés
d'encastage, ou d'arrangement des pièces
dans les fourneaux.
- Les qualités de la
porcelaine dure sont de pouvoir résister sans
fracture aux changements brusques de
température quand ils s'étendent de 0
à 100 degrés, et de pouvoir être
portée à une plus haute
température sans se briser quand on prend les
précautions convenables ; c'est ainsi que la
porcelaine peut être employée longtemps
à tous les usages domestiques, et
exposée même aux températures
hautes et variables des laboratoires de chimie. C'est
sa première qualité, sa qualité
fondamentale.
- Les autres qualités,
pour être moins importantes, n'en sont pas moins
recherchées. On veut que la pâte soit
blanche, d'un blanc de lait, sans taches, que le
vernis offre une surface glacée et unie, sans
ondulations ni points enfoncés ; que les
pièces présentent avec pureté,
avec finesse même, les formes et les contours
qu'on a voulu leur donner ; enfin qu'elles n'aient ni
l'épaisseur, ni les formes
émoussées de la
faïence.
- La France a pour la
fabrication de la porcelaine dure un avantage
fondamental, celui de la matière
première. Son kaolin de Saint-Yrieix,
près Limoges, est plus pur qu'aucun autre
kaolin connu ; à cet cause de
supériorité s'ajoute celle du goût
et des arts du dessin. Ainsi s'expliquent les
progrès croissants de cette belle industrie
parmi nous.
- La pâte de porcelaine
dure dans les fabriques de Paris et du Limousin est
composée de quatre parties de kaolin non
lavé, et d'une de feldspath. La pâte,
dite de service, de la manufacture de
Sèvres, contient sur 100 parties, 64 de kaolin
lavé, 6 de craie de Bougival, 10 de sable pur
d'Aumont, près Chantilly, 10 de sable du lavage
du kaolin. Ce lavage du kaolin, pratiqué
à Sèvres, lui enlève tout le
sable qu'il contient ; il en résulte que les
pâtes de Sèvres sont plus argileuses que
les pâtes de Paris ; suivant Monsieur
Brongniart, elles sont plus susceptibles d'ondulations
ou de déformations à la cuisson, mais
plus propres aussi à donner de grandes
pièces.
- Quant au divers
procédés de moulage et encastage, nous
en devons renvoyer la description compliquée,
mais pleine d'intérêt, à la partie
de notre ouvrage où nous traiterons des
ateliers.
- Les porcelaines dures sont
susceptibles d'un genre de décoration en
couleur que les autres poteries ne présentent
pas d'une manière aussi tranchée : ce
sont les fonds de couleur que l'on appelle au grand
feu. Ces couleurs sont celles qui peuvent
résister sans altération à la
température nécessaire pour cuire le
vernis, émaux et couvertes. Ces couleurs
pénètrent dans l'enduit ramolli, et
acquièrent ainsi un glacé plus profond
et plus complet. Les couleurs qui peuvent supporter le
grand feu dans la fabrication de la porcelaine, sans
perdre de leur nuance et de la vivacité de leur
ton, sont le bleu de cobalt, les verts de chrome, les
bruns dits écailles. Ces couleurs sont
placées sur la porcelaine après qu'elle
est cuite, et par conséquent qu'elle a sa
couverte ; elles repassent au feu. Plus le feu est
vif, et plus ces fonds, surtout le fond bleu, sont
fleuris et glacés. Un feu languissant y fait
naître des défauts nombreux ; les fonds
deviennent louches, plombés,
bouillonnés. La porcelaine susceptible de
supporter la haute température, est donc aussi
celle qui présentera les fonds au grand feu les
plus beaux.
- La Saxe fabrique aussi des
porcelaines dures. Sa fabrication se distingue de la
nôtre par la composition de sa pâte et de
la couverte dans laquelle il entre du gypse que nous
n'y mettons pas. La couverte a un blanc laiteux et
glacé un peu différent de celui des
porcelaines françaises. On place souvent de
petits ornements en bleu de cobalt sur la pièce
après quelle a été
dégourdie, puis on passe la pièce
à un feu modéré pour enlever
l'essence dans laquelle la couleur était
dissoute, on met la couverte par immersion, et on
cuit. Ces ornements bleus se trouvent ainsi comme
fondus et épanchés dans la couverte ;
ils ont plus d'éclat, mais moins de
netteté.
- Vienne, Frankenthal,
Louisbourg près de Stuttgart, Nymphenbourg
près Munich, fabriquent d'après des
procédés analogues.
-
- La Porcelaine
tendre :
-
- La porcelaine tendre est
plus vitreuse, plus translucide que la porcelaine
dure. Sa pâte renferme plus d'alcali, de soude,
de potasse, ou bien des sels à base terreuse,
sulfate ou phosphate de chaux ou de baryte, qui
ajoutés à ses éléments
terreux, l'argile ou le feldspath, forment des
composés assez fusibles.
- La cuisson est double ; on
cuit d'abord le biscuit, et, comme dans cette cuisson
on va jusqu'au ramollissement, il faut que les
pièces puissent cuire les unes dans les autres,
de manière à se soutenir mutuellement,
ou bien on les cuit sur des espèces de noyaux
appelés renversoirs, qui conservent les
formes des pièces, et sur lesquels elles
peuvent prendre leur retraite sans
obstacle.
- Le vernis est mis ensuite ;
il n'a pas besoin d'une aussi haute température
que le biscuit.
- L'Angleterre fabrique une
sorte de porcelaine tendre qu'elle appelle iron stone
china (porcelaine de fer) qui tient presque
également de la porcelaine dure et de la
faïence fine ; elle se distingue de la
première parce que sa pâte est plus
fusible et son vernis plombifère, et de la
seconde parce que sa pâte est transparente et
son vernis plus dur.
- La cuisson de cette
porcelaine est double, et se fait comme celle de la
faïence fine.
-
- Appellations
:
- Porcelaine opaque :
nom donné à la faïence fine de
Montereau, imitant la porcelaine de fer (iron stone
china) de l'Angleterre. C'est en fait une faïence
dure.
-
-
-
-
-
-
-
- Smart2000.fr
©
Mars 2004
-
FRANCE
- Écrit
et documenté par le propriétaire du site
// Contact : Smart2000@wanadoo.fr
- Document
pour CONSULTATION PRIVÉE uniquement - Toute
reproduction totale ou partielle est
interdite
-
-
-
-
- Smart2000.fr
le site
dédié aux passionnés de
céramique
-
- Smart2000
- FRANCE sur https://smart2000.fr/
-
- This
entire page Copyright © 2004-2023, All Rights
Reserved.
- Les
textes et les photos restent la
propriété de leur auteurs, ils ne
peuvent être réutilisés sans un
accord préalable. Nous
consulter.
|